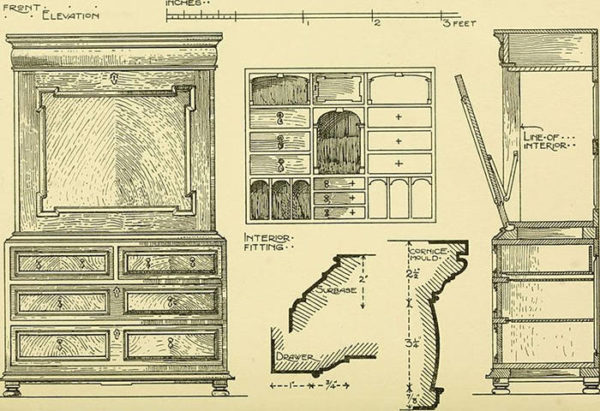
We interviewed DIY experts about their favorite practical advice for beginners who want to make furniture for their homes.
Dale Barnard (the-cabinetmaker.com): My quick answer would be to take a beginning class for furniture making by an older instructor who has been actually making furniture for a living and not just teaching and writing. Also learn the material, as to wood technology about drying, movement, etc. Also be aware that magazines cater to advertisers, and don’t fall for every gimmick and fad that comes along. Be careful about purchasing expensive hand tools, for the same price as a few new hand planes you can get a very good used jointer which will do a thousand times the work in 1/100 the time. Read everything you can by guys with 40 plus years experience.
Danny Kamerath (dannykamerath.com): I have two pieces of advice for the beginning furniture maker: First, select a design or make a design that will not go out of style. If you make trendy furniture, it will look dated in a few years and why go to all the trouble of making something that isn’t going to look good in your home for a long time. Second, and my most important piece of advice for the beginning furniture maker is be stubborn. It is not patience that gets one to the top of a mountain or the end of a marathon or looking at a beautifully executed dovetail, it is stubbornness. Don’t let the setbacks dissuade you. Don’t let the time it takes to make good furniture turn you away from your goal. Making a piece of furniture will take longer than you expected and will likely cost more in materials that you wanted to spend. But it will all be worth it in the end if you are stubborn enough to see it through.
Joe Zeh a.k.a Chiefwoodworker (www.srww.com): 1. Make a commitment to want to be good at furniture making and wanting to make good furniture. 2. For every project you intend to build be sure to have a plan to work from. Nothing is more frustrating to the beginner than a piece that doesn’t work, or wasted material. Buy a plan or create your own with a drawing package like SketchUp. 3. Learn to use hand tools from the very beginning. They are more precise and a lot more rewarding. There is nothing more rewarding than showing off your hand cut dovetails. Hand planes are much quieter than a jointer and much more rewarding. I am not saying ‘Don’t use power tools’. By all means use them, particularly for the initial or rough cut, but real craftsmanship comes from the hand tools. Panel glue ups should always start with finished edges by hand plane just prior to gluing. 4. Take it one cut at a time. The most ornate grandfather clock is withing your capability if you avoid intimidation by breaking the work down into one cut at a time. Subscribe to the major woodworking magazines and watch the DIY woodworking shows. You can learn a lot from the pros and even more from the best hobbyists (who often are the best woodworkers). 5. Practice, practice, practice. If you want to learn to cut your own dovetails practice cutting to a line; over and over and over. 6. Look at other woodworkers work and create a woodworking network to learn from. Most woodworkers do the same and develop good practices. Some don’t. Avoid those woodworkers. Also, don’t look to commercial furniture manufacturers for furniture techniques. Their techniques are most often optimized for low cost, high volume manufacturer which is antithetical to fine woodworking. Studying antiques for good technique is a mixed bag. Many pieces were built by the best craftsman the world has ever produced. But some pieces demonstrate a lack of fine woodworking knowledge. Use your head and always question why something was done the way it was. 7. Let woodworking be fun and never treat it as a chore to be completed.
Matthew Paré Founder (www.petrelfurniture.com): Making something functional for your home is a joy, it has a purity of purpose and if done well, should bring much pleasure both in the making and in its use. Make for the future in mind, this project could become a cherished family heirloom. Here are a few tips on making from our professional workshop, I hope they inspire you to become craftsmen and women for the home. Design simply with purpose and form in mind, don’t over complicate the process for the sake of ambition. One fine handmade details speaks louder than a hundred machined parts. Make a model out of scrap stock, check form, proportions and usability. Select materials well, a local hardwood with character and a story is far more interesting than shop brought generic timber. Treat materials and tools with respect, it is our responsibility to be economical and resourceful. And finally, make with precision and care, take your time. We live in a world where we expect instant gratification, this is often an empty meal. Take your time, design well, sweat in the making and then enjoy the rewards for years to come.
Robert Spangler (rspangler.com): “Take a class”. This will help with the basics (and safety). Please don’t forget the safety part. After a class the beginner will have much more confidence in not only where to start but also will have a better understanding of appropriate joinery for the task at hand. I was asked to teach a class for some beginners one time and I ask them what they wanted. They all agreed that a class on gluing would be good and I thought that was a fairly “dumb” idea for a class but agreed to go ahead. That class turned out to be one of the best classes that I have taught in regards to getting them started. Professionals will often take a lot of things for granted and forget that there are some very basic questions and hurdles that need to be overcome at the beginning. Beginners will often want to cut the perfect dovetail at the beginning without any understanding of basics of the material used, the appropriate joinery for the job or even what glue to use. Woodworking and furniture making in particular is a skill that requires a lot of practice and years to perfect.
Tobias Dean (www.tobiasdean.com): I was struck by your phrasing of the question because while I really wanted to “make furniture” I always thought of it as a way to live, making furniture for others with the assumption that I would make some for myself (such as the pieces that never sold in a gallery and ended up in the living room). However, I applaud anyone interested in pursuing furniture making as a hobby and would love to be supportive of anyone trying to learn about it. As far as “tips” and “tricks” go, can’t offer much in the tricks department. Woodworking takes time, and the more time you are able to spend the higher quality the results will be. That’s not to say that there can be compromises and shortcuts that can reduce the time. For instance more expensive and specialized tools can speed up processes. I would love to own a wide belt sander, or even a drum sander but I make do with a good quality random orbit sander and hand planes. Strictly speaking one can get by with just traditional hand planes and scrapers and sheets of sandpaper but that takes real dedication and time to studying how to use them. And some sanding marks or other defects are not the end of the world as you start out. I would suggest two things a beginner should pay attention to: a sturdy work surface at a height that works well for your body, and learning about sharpening. It all starts at the bench, it would be nice to have a vice or at least a clamp or holdfast to firmly hold your workpiece. (in time you may want to build or buy a proper cabinetmakers bench, but remember that traditional Japanese woodworkers used the floor, their feet and a post to hold work). The best tools wont be much help if you don’t know how to set them up and keep them sharp. I learned first by trying things on my own and reading books, and then later on going to furniture design schools. Now Youtube offers amazingly well done videos and there are numerous online forums that really dig into the craft. If you are really starting out from scratch I would suggest buying a cordless drill/driver for boring holes and driving screws. It is hard to imagine surviving anywhere without one of those. Finally, I am a big believer in learning form other people in person. If you hear about a person like me, getting on in years with a shop, there is a good chance they would welcome some broom wielding company for conversation and passing along some knowledge and giving guidance. I know I can be talked into the shop on the weekends, so just ask. Perhaps they would be amenable to an exchange of a little cash for some tutoring. And go to trade shows, woodworking stores and events if you are able.